Hydroforming Defined: High-Pressure Fluid Meets Metal Precision
Metal forming has come a long way over the years. From hammering by hand to massive industrial presses, we’ve constantly developed new ways to shape metal. Among these innovations, hydroforming stands out as one of the most versatile and precise methods available today. Here, we break down what is hydroforming, what it’s used for, and how it can benefit manufacturers in a variety of industries.
Hydroforming 101: How High-Pressure Fluid Creates Complex Metal Parts
So, what is hydroforming? At its core, hydroforming uses fluid pressure to shape metal. When a piece of metal enters a hydroforming press, it undergoes a transformation unlike any other forming process.
The metal blank gets positioned over a shaped tool, then a flexible diaphragm filled with fluid (usually oil) presses against it with incredible force—sometimes up to 10,000 psi. This hydraulic pressure molds the metal against the tool while the tool is driving up into the part, creating complex shapes that would be nearly impossible with conventional methods.
The history of this technique stretches back more than a century. Early experiments with fluid pressure forming began in the early 1900s, but the process really took off during the mid-20th century as industrial applications demanded more complex parts with better finish quality.
What makes hydroforming special isn’t just how it works—it’s what it can create. Parts come out with exceptional surface finish, consistent thickness, and precise dimensions. Given everything hydroforming can accomplish, it’s no wonder so many industries have embraced this method for their most challenging components.
The Hydroforming Process
Hydroforming is a cost-effective way to produce smaller quantities of drawn parts or parts with asymmetrical or irregular contours that do not lend themselves to stamping. Virtually all metals capable of being cold formed can be hydroformed, including aluminum, brass, carbon, stainless steel, copper, and high-strength alloys.
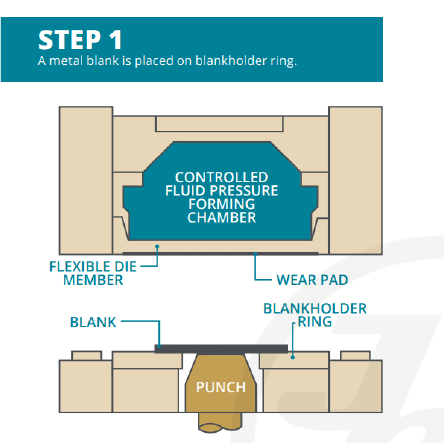
A hydroforming press operates like the upper or female die element. This consists of a pressurized forming chamber of oil, a rubber diaphragm and a wear pad. The lower or male die element, is replaced by a punch and ring. The punch is attached to a hydraulic piston, and the blank holder, or ring, which surrounds the punch.
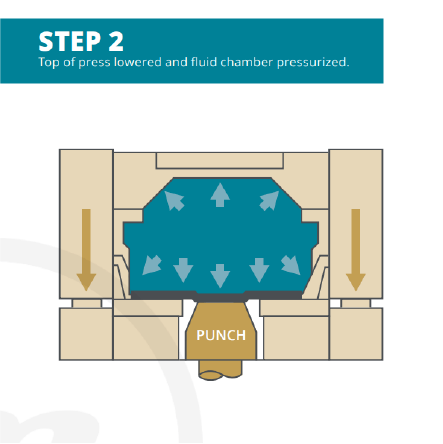
The hydroforming process begins by placing a metal blank on the ring. The press is closed bringing the chamber of oil down on top of the blank. The forming chamber is pressurized with oil while the punch is raised through the ring and into the the forming chamber. Since the female portion of this forming method is rubber, the blank is formed without the scratches associated with stamping.
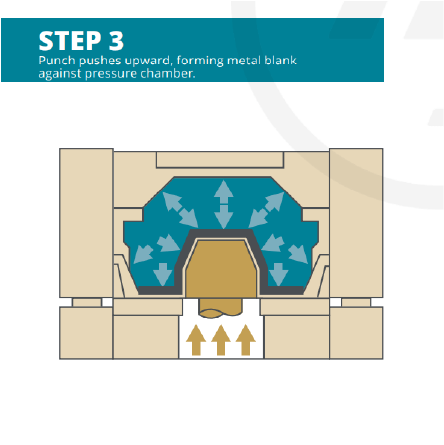
The diaphragm supports the entire surface of the blank. It forms the blank around the rising punch, and the blank takes on the shape of the punch.
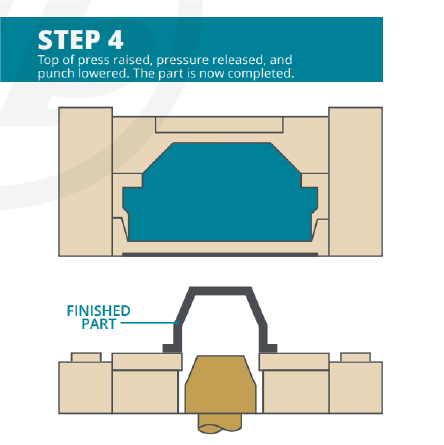
When the hydroforming cycle is complete, the pressure in the forming chamber is released and the punch is retracted from the finished part.
What Metals Can Be Hydroformed?
While hydroforming works with most ductile metals, some materials perform better than others. The ideal candidates share certain properties: good formability, consistent material thickness, and appropriate ductility.
Aluminum alloys rank among the most commonly hydroformed metals. Their relatively low yield strength combined with good elongation properties makes them perfect candidates. From 2024 to 7075 and beyond, aluminum responds beautifully to hydroforming, creating lightweight yet strong components.
Stainless steel varieties like 304, 316, and 409 also hydroform exceptionally well. Their corrosion resistance remains intact throughout the process, making them ideal for medical, food processing, and chemical applications.
More exotic metals also find their way into hydroforming presses. Inconel, titanium, and high-nickel alloys that would challenge traditional metal forming methods can be shaped successfully with the right hydroforming setup.
Copper, brass, and bronze, with their excellent ductility, are perfect candidates for complex hydroformed shapes.
The full list of hydroforming-compatible materials includes:
- Aluminum in numerous grades
- Brass and bronze
- Carbon and stainless steels
- Copper and cobalt
- Clad metals
- Galvanized materials
- Hastelloy
- High-nickel alloys
- Inconel
- Kovar
- Lead
- Molybdenum
- Various titanium grades
Each material brings unique characteristics to the hydroforming process, requiring adjustments to pressure, tooling design, and cycle time to achieve optimal results. At Jones Metal, we have the ability to customize volume production from a single part to thousands of parts depending on your needs.
What Are The Advantages Of Hydroforming?
Hydroforming offers numerous advantages, including:
- Inexpensive tooling costs.
- Reduced set-up time.
- Lower development costs.
- No shock lines, draw marks, wrinkling, or tearing.
- Minimized material thin-out.
- Replace multiple conventional draw operations with one cycle of hydroforming.
- Ideal for complex shapes and irregular contours.
- Optimize material and blank thickness to achieve cost savings.
The Cost Benefits Of Hydroforming Vs. Stamping
Hydroforming metal is a cost-effective method of shaping asymmetrical parts. It is an effective alternative to traditional stamping, increasing efficiency and saving time throughout manufacturing processes.
Hydroforming tends to be cheaper than deep draw stamping because tooling costs are up to 50% less, and the presses only require one cycle. There’s also no need to create new tooling when a change in wall thickness specifications or materials is needed.
The hydroforming process also helps manufacturers save money by the ability to pre-polish the material prior to forming. Since the material is formed by pressure from a rubber diaphragm, it limits scratches and wrinkles on the formed metal parts.
The hydroforming method is extremely precise and can also help reduce material waste. Depending on the material and shape, ID measurements can be held as tight as ±.005 inches if required.
How To Choose The Right Cold-Forming Method
Companies that need to create metal parts may wonder which cold-forming process is the most cost-effective choice: stamping or deep draw hydroforming. Both methods create durable parts, but they’re very different.
When customers aren’t sure which cold-forming process to choose, they should consider the type of part being formed and its specific application. The general rule is that complex, asymmetrical shapes in small runs are better suited to hydroforming. However, stamping is most likely the most cost-effective choice for parts with deep, simple shapes that need to be created in larger batches over 10,000 pieces.
Is Hydroforming Right for Your Application?
Although the hydroforming process has numerous advantages over matched die drawing, there are cases where deep draw stamping may be a better fit for your specific application. In addition to being one of the nation’s largest contract hydroformers, we also have deep draw stamping capability to 350 tons. Contact Jones Metal today and our engineering team will explain the benefits of both metal forming processes and help you select the most cost-effective means to manufacture your parts.