Hydroforming Company Since 1923
When metal needs to take on complex shapes while maintaining structural integrity, hydroforming is an excellent option. This specialized metal forming process uses fluid pressure—up to 10,000 psi—to transform flat metal into precision components with exceptional surface quality.
At Jones Metal Products, we’ve spent over 100 years perfecting our hydroforming services. As America’s largest single deep-draw hydroformer, we’ve built our reputation on solving the metal forming challenges that other manufacturers can’t. Our approach combines old-school craftsmanship with cutting-edge technology. When engineers face seemingly impossible manufacturing hurdles, they turn to Jones Metal for solutions that deliver both technical excellence and cost efficiency.
Benefits of Choosing Jones Metal as Your Hydroforming Company
- Operating since 1923 with over 100 years of experience creating complex metal parts
- NADCAO, ISO 9001:2015, and AS9100:2016 certified, ensuring consistent quality in our metal forming processes
- The largest single deep-draw hydroformer in the country
- Ability to form irregular pieces with all types of shapes and angles with minimal thin-out
- Parts emerge with near-perfect finish free of burrs or scuffs, eliminating the need for finishing or polishing
- Reduce upfront costs by eliminating expensive dies required in traditional metal forming
- Capability to handle both small and large-volume orders
- Ideal process for prototyping with quick, inexpensive adjustments for part development
- Dedicated testing equipment to ensure quality
Let’s Work Together
Please fill our your information below and we will reach out within 24 hours.
Is Hydroforming Right For Your Application?
Hydroformed parts come in many shapes, sizes, and specifications. We can hydroform small, medium, and large parts, as well as irregular parts. While most companies in the industry focus on running larger orders at least 10,000 pieces–Jones Metal fulfills orders of any size.
Materials We Can Hydroform
- Aluminum
- Brass
- Bronze
- Stainless Steel, including 304, 316, and 409, 17-4, 17-7
- Clad Metals
- Carbon Steel
- Copper
- Galvanized Metals
- Hastelloy
- High Nickel Alloys
- Inconel
- Kovar
- Lead
- Molybdenum
- Titanium Grade 5, Grade 2, 15-15-15, 15-3-3-3
Our Hydroforming Services
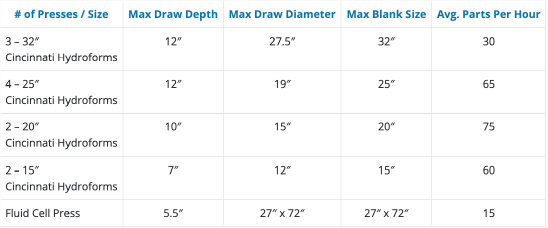
Deep Draw Hydroforming
In addition to offering hydroforming parts with draw depths less than 3”, Jones Metal can also create deep drawn hydroformed parts from blanks up to 32.5” with depths up to 12” and diameters to 27”. We operate at forming pressures up to 10,000 psi, tackling material gauges up to 3/8 inches (steel) and 1 inch (aluminum).
The benefits of deep draw hydroforming metal include many of the same advantages of hydroforming over deep draw stamping and other cold-forming processes, including outstanding surface finishes, reduced tooling costs, and the ability to manufacture parts with irregular shapes while holding exceptionally close tolerances.
Fluid Cell Forming
The ability to manufacture long, deep-drawn, and complex shapes is possible at Jones Metal thanks to our fluid cell forming capabilities available at Jones Metal.
Fluid cell forming is a process that utilizes a fluid-cell press, or bag press, to form sheet metal into complex shapes. The press exerts high pressure, up to 11,600 psi, onto a flexible rubber diaphragm that forms sheet metal into shapes that meet precise tolerances.
Based upon field-proven technology, Jones Metal’s Quintus Technologies Flexform Fluid Cell Press enables the formation of small parts, shallow components, large panels, and complex deep-drawn shapes, such as a negative lip. Several parts can be formed at once in each tray, resulting in significantly faster prototyping, shorter lead times, and lower tooling costs.
As with hydroforming, our fluid cell press limits surface abrasion, translating into fewer resources spent on downstream finishing. This type of forming also enables parts that are thinner, yet still strong.
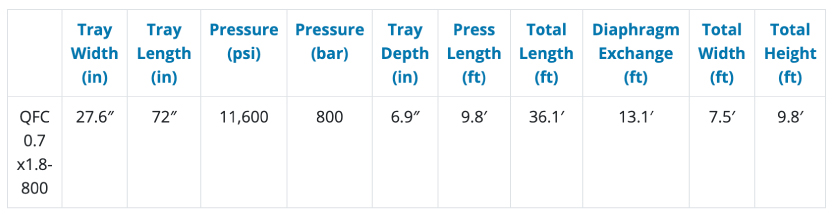
Frequently Asked Questions About Hydroforming
We currently form material as thin as .005” and as thick as 1.25”.
One. Hydroforming can be used for very short runs when necessary. It really comes down to cost. The more parts you buy, the cheaper the cost will be per part. Our goal is to build relationships with companies, and sometimes, that starts with just one part. Not every company is willing to do this–that’s part of what sets Jones Metal apart as your hydroforming company.
The hard tooling only touches the inside of the part. The outside of the part is pressed in by a rubber bladder, which does not cause scratching or surface defects. We can also cover the outside of the part with a removable plastic coating. It can be removed after the forming process is completed, leaving a more pristine surface.
Using the deep draw hydroforming presses, you can form up to a 32” diameter blank, 27.5” forming diameter, and 12” deep. With the Fluid Cell Hydroforming press, you can form up to 72” in length.
Contact Us For Your Hydroforming Needs Today
At Jones Metal Products, quality is our top priority. We are dedicated to delivering ultra-precise products to customers on time and within their budget. Our team has deep industry experience and the technical expertise to create precision components. Call us today at (888) 479-9566 or reach us online to send us your drawings to get started with your hydroforming process.